Side welding shop
Starting a bend on a side welded link
Finishing a bend on a side welded link
Using the opener
Closing with the Johnny
Making the first half weld with the Johnny and squabber
Runnering the weld
Setting the stud
Cranking
Knocking down
Scarfing
Laying over
Welding
Dollying
Setting the stud
A. Ewart Chapman painting.
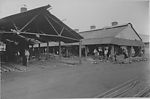
Heavy chains made from 1in (25mm) diameter wrought iron rod upwards, involved a team of men consisting of a chainmaker and several strikers. The number of strikers needed depended on the size of chain being made, from one striker for 1in chain, to three for the heaviest cable chains.
Heavy chainmaking was a job organised into factories, and the work was done on a piecework system, the chainmaker being paid by the firm on a weight basis. The strikers were not employed by the factory, but by the chainmaker, who chose his own men and set the hours to be worked.
Chain from about 2ins (50mm) upwards was welded on the side of the link. Chain less than this was welded at the end. The process of chainmaking consisted of cutting wrought iron bar to length, shaping into a link and welding it together. The welding was done by placing the link into a fire until it reached between 1300 and 1400 degrees celsius, and then hammering the two ends together forcing them to join.
A single link could weigh as much as 1cwt (50.8kgs), and the average weight for a hammer was 13kgs (27 pounds). The skill of the team would be to minimise handling and movement so that energy was saved for the heavy lifting. For all the sizes of chain, the method varied from factory to factory and from chainmaker to chainmaker. Links for the anchor on the S.S. Titanic were made from 6in diameter rod!
The number of links a chainmaker could make depended on his skill, the size and quality of the iron and the quality of the fuel.
Rollover the captions in the box to see the available images in thumbnail format, click the caption to see the full-size image
Reference: | 669 |
Keywords: | |
Archive Ref: | K. Gale Lib 1994/013/1250 |
Updated: | Thu 22 Mar 2007 - 1 |
Interpretation written by | Louis Howe |
Author's organisation | Curatorial |
Organisation's website |