Medium chain shop
Interior medium chain shop
Cranking or bending
Knocking down
Scarfing
Laying over
Welding on face of anvil
Finishing the weld on the anvil point
Dollying with the Oliver Hammer
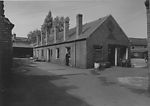
Making chains from about 3/8in (10mm) diameter rod to 1in (25mm) diameter rod was the job of one man, who used a foot operated treadle hammer, the "tommy", to smooth off and consolidate the weld. This section of the trade was carried out both in factories, usually long narrow buildings with hearths down each side, and in smaller domestic workshops which contained only one or two hearths.
Cut lengths of rod were kept near the hearth for pre-heating, and were placed in the hearth to be brought to red heat, while the chainmaker was finishing the previous link. The new link was then removed from the hearth and bent into a āUā shape on the anvil, before being returned to the fire. Once up to red heat again it was removed and the ends of the rod were hammered flat, a process called "scarfing". Again returning the link to the heat, once heated it was removed and threaded through the previous link. The two scarfed ends would then be layed over each other, and the link returned to the fire to be brought to welding temperature, 1300 -1400 degrees celsius. The link was removed from the fire and the two ends hammered together to complete the weld.
At this point the tommy hammer was used to return the rod to its original diameter and smooth out the weld. The tommy hammer had a tool, called a die, fitted into the face of the hammer, which was shaped to match the shape of the rod being used. The new link was placed on the anvil at the point where the hammer would strike, and the chainmaker would operate the tommy by pressing a treadle with his foot bringing down the tommy onto the link with great force. The shaped tool in the tommy would form the still soft iron into the required shape, consolidating the weld, and the link was finished.
The chainmakers were paid piecework, and the number of links a chaimaker could make in a given period depended on his skill, the size and quality of the iron and the quality of the fuel. Breeze, the small pieces of coke used as a fuel for chainmaking, sometimes contained dirt or other impurities, and these would build up in the hearth, until the efficiency of the fire was impaired. The quality of the wrought iron would vary according to the skill of the furnaceman and the number of times the iron had been rolled prior to use. In the case of 1/2in (12mm) chain a link could be made every minute, so eight hours work would produce 480 links. This would bring a weekly income of around 25 shillings (125 pence) in 1913.
Rollover the captions in the box to see the available images in thumbnail format, click the caption to see the full-size image
Reference: | 670 |
Keywords: | |
Archive Ref: | K. Gale Lib 1994/013/1250 |
Updated: | Thu 22 Mar 2007 - 1 |
Interpretation written by | Louis Howe |
Author's organisation | Curatorial |
Organisation's website |