Domestic chain shop
Interior of domestic chain shop
Heating the rod
Cutting to length
Bending in swedge
Laying or turning over on bick-iron (anvil)
Welding
Twisting
A. Ewart Chapman painting.
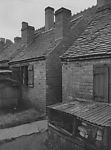
Light chain making was almost exclusively carried out in small domestic workshops attached to the worker’s dwelling house.
The pictures show us Elizabeth Jennings working at her anvil, a job she first began when she was thirteen. The equipment was simple and the chain made was up to 3/8in (10mm) in diameter, mainly for agricultural use and was known as “countrywork”. For this use the finish of the chain was not particularly important, and so it was mostly left with hammer marks. However, light chain may also be used for such items as dog leads, where a finer finish was important, so in such cases, the chain was finished with a dolly.This is a tool, fixed to the anvil, which is shaped to the profile of the rod being used, and placed over the welded link while still hot.
The workshop would have contained a small breeze (coke) fired hearth, hand bellows and the basic hand tools consisting of a small anvil, a "swedge" for bending the iron rod, a "hardy" for cutting the rod to length, a "twister", tongs, two hammers and a water "bosh" for rapid cooling of the ironwork.
Rods were delivered to the shop, usually through the window, in lengths of 10ft to 12 ft.(3m – 3.5m). The end of a length of rod was placed in the fire to bring it up to red heat, a child often being used to operate the bellows or, as it was known, the blast. The length of rod was then laid across the hardy, or cutting off chisel, until it touched the adjustable gauge at the back, and struck with a 2lb (0.907kgs) hammer over the edge of the hardy. This cutting almost, but not quite, severed the rod. The short piece of rod, still connected to the main length by a thin piece of metal, was then dropped into the slot of the swedge, and the hot part bent around to form the rough link. This process was called cranking, as in the work of the heavier chainmakers.
The rough link, still in the form of a letter “U”, was broken off the rod by a twist of the hand, and threaded through the previous link. The ends were then "scarfed", or flattened, and laid over each other, a process known as laying over or turning over. The end of the link was then raised to welding heat in the fire and welded, or shut, on the anvil using a 1 1/2lb (0.68kgs) hammer.
If the chain was required to lay flat, as would be the case for an animal harness in order to be more comfortable for the animal, the end of the still hot link was placed in the "bender" and the link was twisted through 90 degrees.
If the chain needed a finer finish, for a dog chain for example, the hammer marks in the link would have been removed by the use of a dolly, which would smooth out all trace of the hammer marks.
The varieties of chain produced in this way was extensive, the manufacturer Samual Lewis & Co. listing over 140 types in its catalogue.
Rollover the captions in the box to see the available images in thumbnail format, click the caption to see the full-size image
Reference: | 671 |
Keywords: | |
Archive Ref: | K. Gale Lib 1994/013/1250 |
Updated: | Wed 21 Mar 2007 - 1 |
Interpretation written by | Louis Howe |
Author's organisation | Curatorial |
Organisation's website |